INTERVENTION AT THE INTERFACE OF
MULTIPHASE DISPERSED SYSTEMS
Author
J. Mark Chandler
President of ACT Solutions Corp
www.ACTSolutionsCorp.com
ABSTRACT
Often we are asked to dig deeper and not simply look for superficial answers to life’s problems. While this is generally good advice, for the formulating cosmetic chemist, this is not always the best advice. For these creative specialists the answers lay on the surface and in the surface-active agents (surfactants) necessarily employed in most cosmetic and personal care products. Without surfactants, there is no cosmetic industry. We would be left with smearing oils and colors on our bodies, and relying on water alone to clean us up. What a mess!
Surfactants are not only the key to cleansing hair and skin, but are of paramount importance in producing the desired and required aesthetics of formulations of all types and in all categories. Personal care products provide an important function for acceptance in our culture in terms of achieving a person’s cleanliness and perception of beauty. These functions are crucial elements of the role of personal care products in society, but there is much more. A cosmetic product, whether it be a shampoo, skin cream, or antiperspirant, is a luxury item. Luxury items are about an experience as much as, if not more so than, an effect. In order to be successful, a personal care item must not only function, it must excite! In view of this elemental truth, proper understanding and use of these small but powerful interfacial components is a key to the commercial success of a formulation.
Understanding all of the physical/chemical aspects of surfactants is not critical to successful use of these materials. However, a background and understanding of these aspects are interesting nonetheless, and can help unlock some of the mysteries of their impact and activity on product development approaches. This chapter will first provide an introduction to the world of surfactants, and then move quickly into the specific functions that surfactants perform in key application areas. Following this, a step back will be taken to look at a more detailed description of the physical/chemical aspects of how surfactants work. The chapter will conclude with a more in-depth view of the chemistry of the more important surfactants in use today and provide a glimpse into their future in the personal care industry.
4.1.10 Surfactant Introduction
4.1.12 Applications: A Look at Some of the Many
4.1.10 SURFACTANT INTRODUCTION
Surfactants have been used for several millennia. Early mention of the use of soap, a naturally derived anionic surfactant, comes from the Akkadians around 2800 bce. This surfactant was manufactured by boiling fats with ashes, and used for cleaning wool and cotton in textile production. Other early applications employed by Mesopotamians for soap was cooking utensil cleaning and treatment of skin diseases. Later the Phoenicians spread this surfactant-producing technology to Egypt and later to Gaul (today France). With the Roman conquest of Gaul, soap production became very important for use in the elaborate public baths. A full-scale soap-production facility (though no reliable production data exist) located in Pompeii was unearthed, dating back to the volcanic eruption that destroyed the city in 79 ce. Location of the facility was likely due to the ready availability of the raw material, ash, and the fact that Pompeii was a resort city.
With the fall of the Roman Empire, soap production appeared to fall considerably until around the tenth century. Not only were they the Dark Ages, they were also dirty. Soap was an item of commerce and trade, produced best by those in Italy and France, and sold around the world, though only the wealthy could afford this luxury item. In other areas, soap-making was a local or home craft. By the 17th century, many large towns had soap-boiling operations, and by 1850, commercial soap-making for the masses was established by such companies as Colgate (1).
The first nonionic surfactants came onto the scene in the 1930s, developed by the Atlas Powder Company in Delaware. Using waste sorbitol made as a by-product of mannitol production and reacting with long-chain fatty acids, the sorbitan ester surfactants were produced. In the 1940s, these oil-soluble materials were made more hydrophilic by the binding of a polyethylene oxide chain onto the molecule. For instruction on how to use these novel surfactants, which have a character much different than soap, William C. Griffin designed the HLB system. Since then, hoards of new anionic, amphoteric, and cationic surfactants have been invented and put into wide-scale use, making for a cleaner, safer, and more pleasant world.
The word “surfactant” is a shortening of the term “surface active agent.” Surfactants’ work is done at interfaces. The molecules are called amphiphilic, because they are attracted to two different characters of materials. Most often, one part of the molecule is hydrophilic, or water-loving. This portion is also call the polar head group. The other portion of this amphiphilic molecule is hydrophobic, meaning that it is uncomfortable in water. These surfactants break down the interfacial tension between substances, one of them usually being water, and the other air, immiscible liquids, or solids. The ability of surfactants to have a dual affinity makes them uniquely placed to perform a variety of useful functions in personal care products.
Creams and lotions are not formed or stabilized easily without the use of surfactants. Cleansing hair, face, and body is extremely difficult without the use of surfactants. Hair conditioners, makeup, and deodorants would be in a sad state without surfactants. It must be remembered that personal care items are much more than just technical items designed for a specific function on the skin or hair. All of these products are as much about the emotional experience as about the specific task. Thus personal care items are luxury goods, not unlike cars and electronics, regardless of price point. Who would buy (well, at least more than once) a lotion that stayed separated, a cream that felt terrible, or a shampoo that did not foam? All of these products could do the job technically, but would leave the consumer dissatisfied and looking elsewhere. A great many of the positive emotional cues we receive from use of our personal care products, whether they be performance or aesthetic, are the result of clever use of surfactants.
There are hundreds of different surfactant chemistries from which to choose for a given personal care application. All of them fall into four basic categories, based on charge behavior (no, not how much the suppliers charge for these wonderful materials!). The original surfactants, soaps, belong to the greater category of anionic surfactants. These surfactants possess a net negative charge. The second group, mentioned in the History section, fall into the category of nonionic surfactants. These molecules have no charge, except when being purchased. A third group is called cationic, for they have a net positive charge. The last group is termed amphoteric, meaning the surfactant changes charge character based on the pH of the system (2).
This is likely the most complex of the surfactant functions. Recent research indicates strongly that the selection of emulsifier and emulsion stabilizer is of great importance to the overall aesthetics of a cream or lotion. Much work is involved in formulating an emulsion. Surfactants play a key role in the two main steps involved making these high value systems for the face, hand, and body. First, there is the step of droplet creation. This can be accomplished with mechanical energy such as mixing, but aided greatly through the judicious use of surfactants, which reduce the interfacial tension between the immiscible oils and water. The second step is to stabilize these droplets against aggregation, creaming or sedimentation, Ostwald ripening, and coalescence. Density differences between phases and Van der Waals forces tend to work against these kinetically stable but thermodynamically unstable systems.
There are four main stabilization mechanisms used to produce personal care emulsions. The first is charge, or ionic stabilization. The second is nonionic, or steric stabilization. A third is stabilization based on the formation of liquid crystalline lamellar phases, and the last but not least is polymeric stabilization. Each places different demands on surfactants, and requires different formulation and manufacturing techniques. Each has advantages and disadvantages, and is seldom used in isolation.
With charge stabilization, an ionic double layer is formed around the emulsion droplet. This creates electrical repulsion with surrounding droplets, slowing emulsion instability. This can be accomplished with anionic surfactants like soaps or phosphate esters, or, less commonly, with cationic surfactants. This mechanism is almost exclusively used in oil-in-water emulsions. Very often charge stabilization is used along with steric, polymeric, and liquid crystalline stabilization. Soaps are generally formed during the formulation process through the neutralization of such long-chain fatty acids as stearic acid with sodium hydroxide or TEA. The pH of soap-stabilized systems must be above 7, which makes them irrelevant for emulsions containing alpha or beta hydroxyl acids. Phosphate esters and cationics have greater pH tolerance. As a general rule, cationic and anionic surfactants have the highest irritation potential when compared to other surfactant types, but low-irritation skin care emulsions can be formulated with judicious use of these materials.
Using nonionic emulsifiers to engineer steric stabilization of droplets requires the most formulation work to optimize, but these emulsions are generally best able to withstand the harshest formulation challenges placed on them. These challenges include low and high pH, high electrolyte levels, low and high internal phases, varying oil polarities, and combinations thereof. These emulsions must be designed such that there is a very consistent and flexible film of emulsifier around the droplets. The simple HLB system was designed to ensure maximum packing of emulsifier through tuning the ratio of hydrophilic to lipophilic surfactant based on the specific requirement of the oil phase selected.
Surfactants consist partly of the molecule that is hydrophilic, or water loving, and partly of the molecule that is hydrophobic. An HLB value is assigned to nonionic surfactants based on the weight percentage of the molecule that is hydrophilic, then dividing that number by five. For instance, a surfactant such as Steareth-20 has a hydrophilic polar head group that is 75% of the weight of the total molecule, and the HLB value is deemed to be 15 (75 / 5 = 15). The higher the HLB, the more hydrophilic the surfactant is. Sometimes ionic surfactants are listed with HLB values, but these are of limited usefulness. Surfactants can be combined to give a composite HLB value for the system. The result is purely arithmetic. If an HLB 15 surfactant is combined with another at HLB 5, blended in equal parts, the composite HLB is 10.
Oils to be emulsified have HLB requirements. A simple test will show the required HLB of a given oil or blend of oils. Test blends of surfactants at defined HLB values are prepared, generally using sorbitan oleate (HLB 4.3) and polysorbate 80 (HLB 14.9) blended to even HLB values from 6 through 14. Two grams of each blend are mixed with 20 grams of test oil in a 50 mL glass jar with a top. Water is then added, filling each jar. The jars are capped and hand-shaken 20 times. The emulsion showing the least separation is the winner and recorded as the HLB requirement of the oil. If two of the even HLB blends appear close in stability, the odd-numbered value in between is tested.
Blends of oils have an HLB requirement equal to the sum of the HLB requirements of each oil multiplied by its percentage of the total oil phase. Once the HLB requirement for the oil phase is determined, various chemistries of nonionic surfactants can be evaluated for compatibility, cost, and effectiveness, with the optimum blend ratio already having been determined. For best emulsion stability, a blend of low and high HLB surfactants, each a few HLB units away from the requirement of the oil phase, is preferred.
The HLB system is designed for optimization of steric stabilization using nonionic emulsifiers. Other stabilization mechanisms can be used in addition to enhance emulsion stability. The system works independently of phase/volume ratio, total surfactant level, or chemistry type of ingredients.
Liquid crystalline lamellar phases are surfactant structures built in the aqueous phase either alone or around an emulsion droplet. They are generally made with nonionic surfactants, though some anionic and cationic surfactants have shown useful behavior as well. The structures formed are similar to the lipid bilayers found in the upper layers of the skin, and the surfactants used tend to have low potential for disruption of the skin moisture barrier. The resultant emulsions are reported to possess good resistance to wash-off, and offer enhanced moisturization, reduced evaporation rates, and superior delivery of water-soluble actives. Commercial examples of liquid crystal emulsifiers such as a blend of sorbitan stearate and sorbityl laurate are best utilized by adding the solid product, and any other waxy materials to be used in the formulation, to water heated to 80°C and stirring until a white uniform mixture is obtained. Heat is removed at this point with stirring
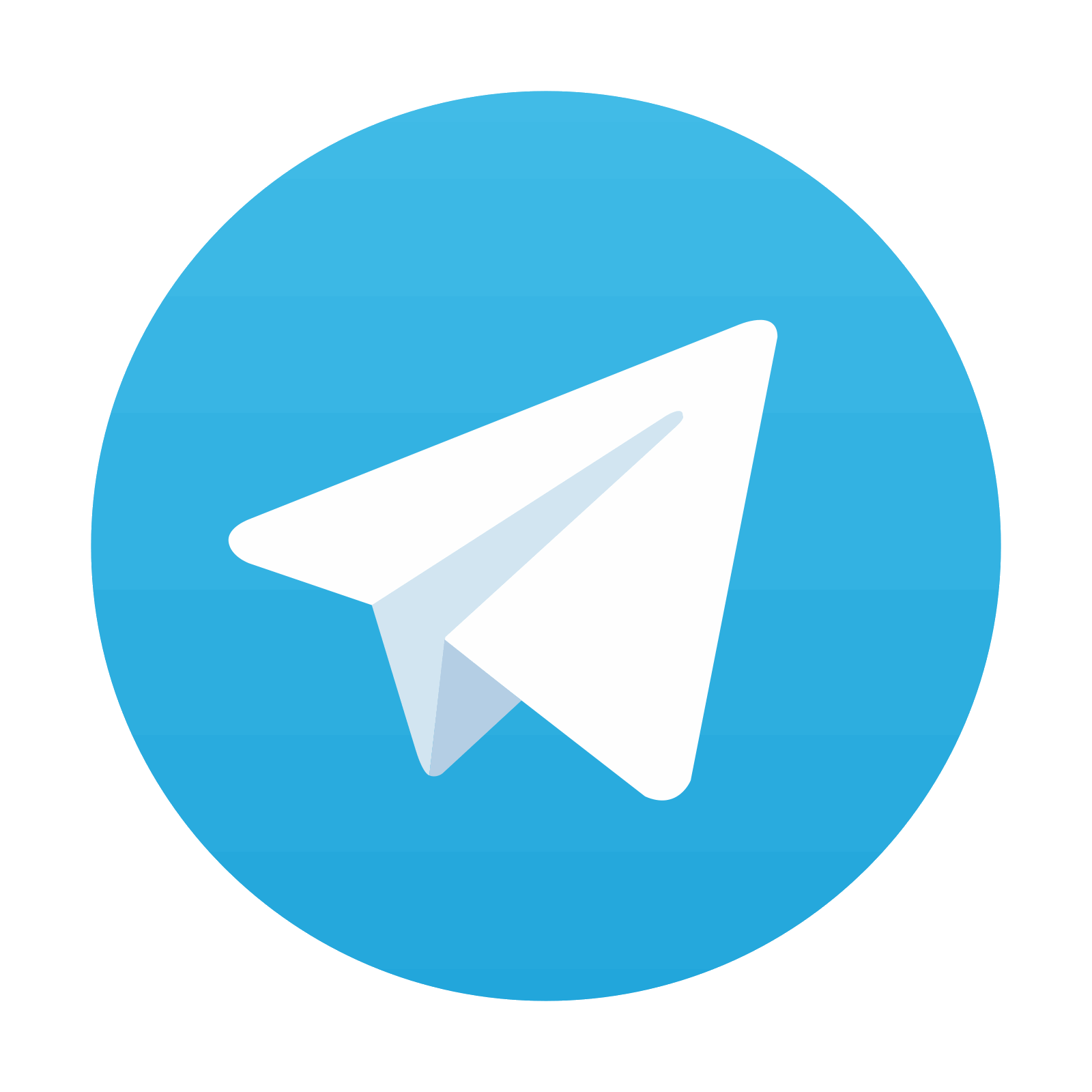
Stay updated, free articles. Join our Telegram channel
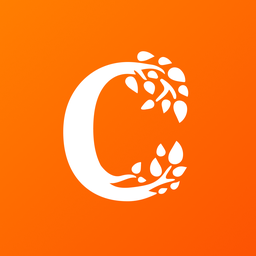
Full access? Get Clinical Tree
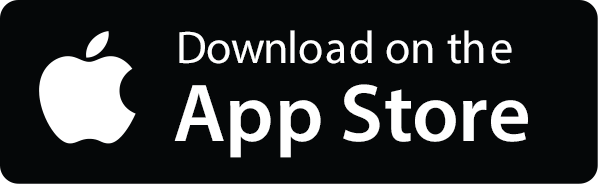
