NATURAL AND SYNTHETIC POLYMERS:
DESIGNING RHEOLOGICAL PROPERTIES
FOR APPLICATIONS
Author
Susan Freers
Grain Processing Corporation
ABSTRACT
There are many rheological additives a formulator may select to obtain the desired properties of the final formulation. Often several rheological additives would perform well in a particular formulation and the formulator must make some choices. Considerations regarding the product application, labeling, consumer targets, and pricing come into play. However, more important considerations are the requirements of processing and the stresses the formulation will encounter. Therefore, the pH of the formulation, the processing temperature and shear rate, the packaging conditions, and the consumer’s handling of the product are extremely important. The formulator must also consider the desired appearance and properties of the final formulation.
Most rheological additives contribute more than controlling basic flow and viscosity properties. Many also provide flow properties, suspension properties, emulsion stabilization, stability to shear, heat, pH, or freeze/thaw cycles, etc. The rheological additives that can be utilized to achieve these properties in various applications are discussed in this chapter, as well as an overview of each of these rheological additive categories.
4.2.1.1 Designing Rheological Behavior
4.2.1.2 Natural and Synthetic Polymers: Rheological Properties
and Applications
4.2.1.3 Rheological additives used to obtain specific properties
4.2.1.4 Rheological additives for aqueous systems
4.2.1.5 Rheological additives for non-aqueous systems
4.2.1.1 DESIGNING RHEOLOGICAL BEHAVIOR
4.2.1.2 NATURAL AND SYNTHETIC POLYMERS: RHEOLOGICAL PROPERTIES AND APPLICATIONS
Natural and synthetic polymers are used in a multitude of formulations to design rheological properties for various applications. This chapter discusses rheological additives for both water-based systems and anhydrous systems. Rheological additives for water-based systems include natural gums and natural gum derivatives, cellulosics, starch derivatives, clays, polyethylene glycols, fatty alcohols, and polymers. Anhydrous systems are more often modified by the use of silicas, polyethylenes, fatty acids, castor oil derivatives, aluminum/magnesium hydroxide stearate, stearic acid derivatives, or organoclay pre-dispersions. Some of these additives are used for both aqueous and nonaqueous formulations.
Most rheological additives contribute more than basic flow and viscosity properties. Many also provide suspension properties, stabilize emulsions, and improve stability to shear, heat, pH, or stability to freeze/thaw cycles. They can also promote penetration, lubricity, and slip and modify the ultimate skinfeel of the finished product. Overall, the addition of rheology modifiers contributes to emulsion stability and improves the shelf life of the product. The rheological additives that can be utilized to achieve these properties in various applications can be split into two categories: additives that can be used to modify water and additives that can be used to modify liquids other than water. Though this basic classification system can be useful, it should be remembered that many cosmetic systems contain both water and oil phases and can therefore use rheological additives from either group, depending on the need.
There are many rheological additives a formulator may select to obtain the desired properties of the final formulation. Often several rheological additives would perform well in a particular formulation and the formulator must make some choices. Considerations regarding the product application, labeling, consumer targets, and pricing come into play. However, more important considerations are the requirements of processing and the stresses the formulation will encounter. Therefore, the pH of the formulation, the processing temperature, shear circumstances, the packaging conditions, and the consumer’s handling of the product are extremely important. The formulator must also consider the desired appearance and properties of the final formulation.
4.2.1.3 RHEOLOGICAL ADDITIVES USED TO
OBTAIN SPECIFIC PROPERTIES
Using a rheological additive to create higher viscosity can greatly contribute to the emulsion stability of the finished formulation and therefore produce a longer product shelf life. These thickeners may be naturally or synthetically derived, organic or inorganic polymers. The effects of product viscosity changing due to changes in pH, temperature, or shear can be stabilized by using the right rheological additive. Thickeners also help to suspend active ingredients or pigments in formulations, such as using carbomers in lotions or organoclays in nail polish. Higher viscosity in formulas, especially skin and hair care products, is often associated with luxuriousness and therefore improved consumer acceptance.
Surfactant systems, such as shampoos, body washes, and shower gels can be very difficult to thicken and stabilize. Typical rheological additives used for these surfactant systems include carbomer, gums, gum derivatives, starch derivatives, aluminum/magnesium hydroxide stearate, hydroxypropylmethylcellulose, or simply salt.
Thixotropic rheology modifiers create viscosity in the formulation; however, when the formulation is applied to the skin or hair, it becomes thin so it can be evenly spread. In other words, these additives can cause the product’s viscosity to decrease when the shear rate is increased. They do not immediately return to their original viscosity when the shear is removed, but the original viscosity will be recovered if given enough time. Therefore, formulators must consider the level of shear to which the formula will be subjected in the laboratory or in the manufacturing environment.
If the rheological additive in the formula is shear-sensitive, such as with large polymers or silicas, then the overall product rheology can be affected. The product structure may break down and the final product will no longer have the intended rheology. On the other hand, rheological modifiers like clays and organoclays and some gums, like carrageenan, thrive on shear and will not break down under these conditions. The viscosity may even build higher with these shear-loving additives.
It is important to be aware of time and temperature when working with thixotropic rheology modifiers. The cooling rate of the product can affect viscosity and structure formation. If one tries to measure the viscosity of a thixotropic material without control of the length of time before testing, one may get results that are not reproducible since the time on the viscosity recovery curve is not controlled. The formulator must also keep these sensitivities in mind when testing and reporting accelerated stability results for products with thixotropic ingredients.
Pseudoplastic rheology modifiers are shear thinning when the shear rate is increased; however, they return to their original viscosity when the shear is removed. Good examples of pseudoplastic rheology modifiers are gums, like xanthan or guar gum. Carbomers, cellulosics, clays, and silicas also exhibit excellent pseudoplastic properties. The rheological additive is often chosen to achieve the desired product attribute when used by the end consumer. For example, a hand lotion may be formulated to rub in quickly, whereas a massage lotion or barrier cream will be formulated to have more play time and rub in slowly.
Rheological additives can increase the resistance to flow or yield value. It is important to have even distribution of the active ingredients, colors, and other additives in the formulation emulsion or suspension. Increasing the yield value can contribute to this stability. Flow properties can make or break consumer acceptance of products like lotions or shampoos. If the desired amount of product is not easily pumped or squeezed out of the package, the product itself may be wonderful, but the consumer may fail to purchase it again. Products like nail polish require good flow properties from their rheological additives to evenly distribute the wet polish on the nail; however, the brush marks must then disappear on the dry polished nail.
Emulsion technology is another key area for the use of rheological additives. Stabilizing emulsions against phase separation can be accomplished with two different rheological approaches: adding a rheological additive to the external phase or adding it to the internal phase. The first approach is the one most frequently used. By choosing an additive that either increases the viscosity of the external phase or introduces a yield value to that phase, the formulator can slow down the flow of the internal phase through the external one. Formulators can also adjust the rheology of the emulsion by incorporating a rheological additive into the internal phase. The stabilizing effect here is caused by making the internal phase more “deformation resistant.” Using an oil-in-water emulsion as an example, a viscosity-increasing additive in the oil phase will make the oil droplets more resistant to deformation as they flow past each other. The harder they are to deform, the harder it will be for the oil phase to flow through the aqueous phase, thereby increasing the time required for creaming, phase separation, or coalescence.
Finished product stability is often a result of ensuring emulsion stability of the formula. Rheological modifiers are key ingredients in providing emulsion stability to formulations such as lotions, sunscreens, or cleansing products. As described above, these ingredients can be added to the internal or external phase, but are most often added to the external phase. They prevent phase separation often by building the viscosity of the product and slowing down the potential flow of one phase through the other.
There are many rheological additives that can be used to stabilize emulsions and often more than one is used in a formula. These additives not only thicken and suspend to stabilize the emulsions, but go beyond that to actually develop a polymer network that keeps the oil droplets from coalescing. Typical rheological modifiers used to stabilize formulas include natural gums and natural gum derivatives, cellulosic derivatives, starch derivatives, clays, fatty alcohols, synthetic polymers, or silicas. For example, synthetic polymers are often used for emulsion stability in creams and lotions or personal cleansing products. In aqueous systems, starch derivatives inhibit syneresis, which is the separation of water from the formulation. Controlling this moisture migration extends the shelf life of the product by maintaining a stable emulsion.
Insoluble additives are increasingly added to personal care formulations. These additives are often very fine in particle size and have a tendency to settle out of the formulation over time. Rheological modifiers are used to suspend these particles and create a stable product. Suspending agents are rheological additives since they change the rheology of the fluid, making it more difficult for the solid particles to flow through. Many suspending agents form a loosely bound structure within the liquid, and the solids become trapped and are supported in the formula. If the weight of the solid exceeds the strength of the supporting structure, the solid will settle. Therefore, fine particles suspend more easily than very large particles. Antiperspirants, sunscreens, liquid makeups, mascara, and nail polishes all depend on suspending agents to help distribution of active ingredients and pigments. Lipsticks also benefit from suspending agents. When a lipstick is manufactured, it is held in a molten state until it is poured into molds. When melted, it is critical that the pigments stay in uniform suspension; otherwise, some lipsticks of the batch may contain more pigment or color than others. After injecting the hot lipstick mass into a mold, it is also important that the pigment does not settle into the tip of the stick, or the lipstick’s appearance will suffer. Examples of rheological additives that act as suspending agents include natural gums and natural gum derivatives, cellulosics, synthetic polymers, carbomer, starch derivatives, clays, silicas, polyethylenes, castor oil derivatives, and organoclays.
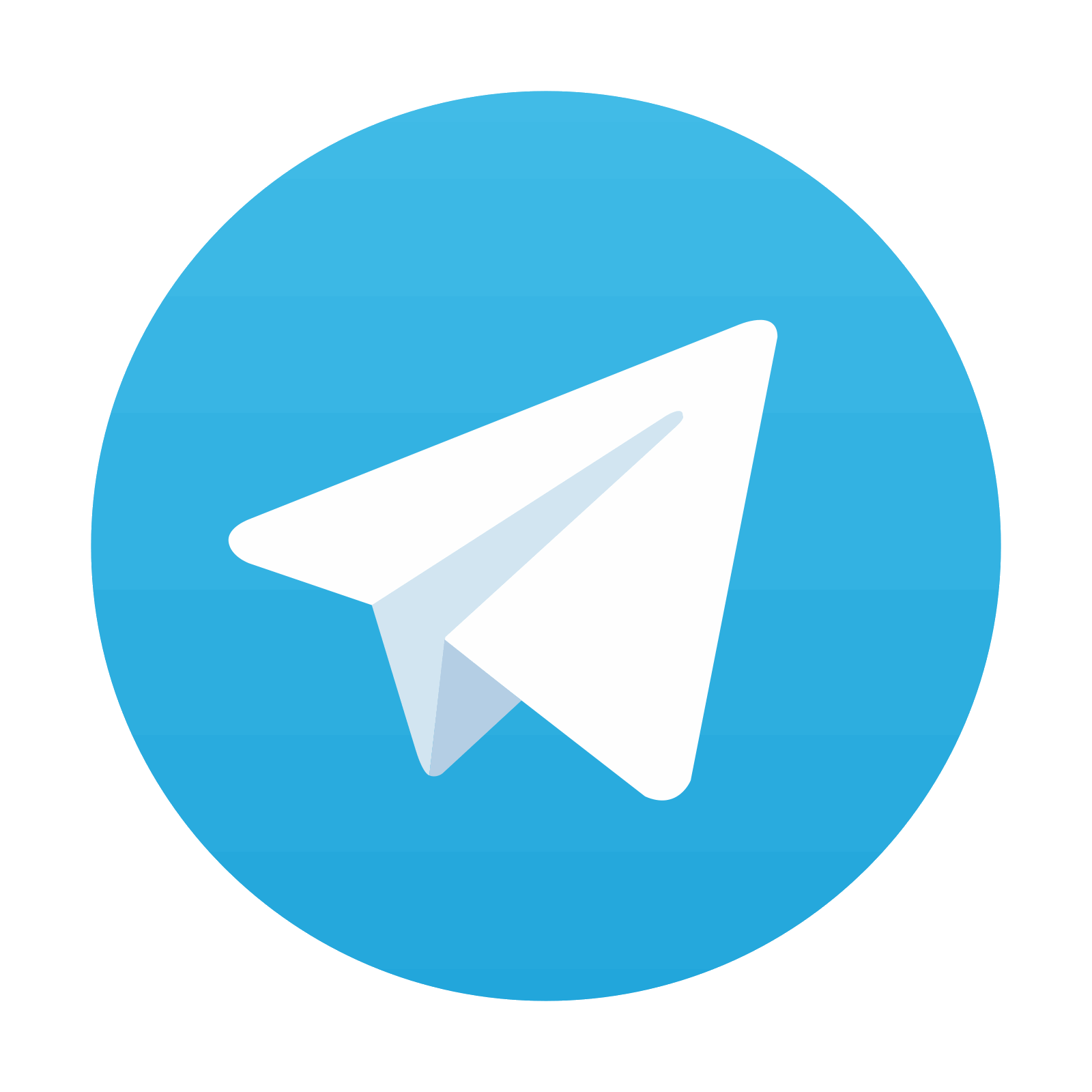
Stay updated, free articles. Join our Telegram channel
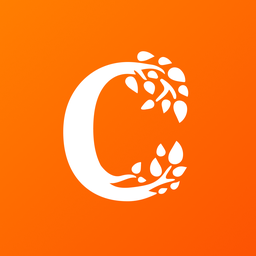
Full access? Get Clinical Tree
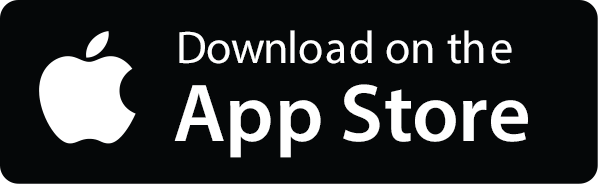
