SUB-MICRON DISPERSIONS:
FORMULATION AND AESTHETIC ENHANCEMENT
OF COSMETIC AND OTC PRODUCTS
Authors
Michael Ross and James Wilmott
Leading Edge Innovations, LLC, 50 Tannery Road, Suite #5,
Branchburg, New Jersey 08876
ABSTRACT:
In view of the trend to reduce costs and increase convenience of emulsion preparation, especially in these days of consumer safety concerns, energy saving focus and environmental consciousness, new technologies are needed to address global concerns. One potential solution utilizes an alternate approach to formulating conventional emulsion-like products. This approach enables cosmetic scientists to prepare personal care and OTC drug products more rapidly and more reproducibly. Unlike conventional emulsions, with typical particle sizes exceeding 3 microns this process generates sub-micron, oil-in-water micelles, which are 1/10th to 1/20th the particle size of conventional emulsions.
Oils and other hydrophobic materials used in these systems have different physical and chemical properties which are distinct from conventional emulsions where the properties of both the oil and water are modified by the nature and quantity of the surface active agent(s) employed. Hydrophobic materials take on very different, desirable tactile properties when the dispersed phase particles are reduced significantly in size. The resulting sub-micron systems can be easily mixed into a rheologically modified matrix and are able to generate either conventional or highly unique tactile experiences. On a laboratory scale, the products are prepared in a single beaker so there is no need for separate sub-phases, and no heating, shearing or cooling is required! This cold-process formulation technique takes from 5 to 15 minutes per batch resulting in a significant improvement in productivity and new opportunities for unconventional product distinctions. This technique can also be readily transferred to the larger scale vessels used in the production of the final product.
13.2.2 Factors Driving the Search for Alternate Approaches
e. Resource Availability and Sustainability
13.2.4 Methods of Producing Sub-Micron Micelles
13.2.5 Formulating with Sub-Micron Micelles
a. Protection of Key Materials
b. Consistency & Reproducibility
b. Unique Aesthetic Experiences
c. Consistency and Reproducibility
In the late 1960s and early 1970s functional skin treatment products emerged. Product performance expanded beyond the amelioration of superficial dryness, and their benefits evolved to a higher therapeutic level. The boundary between cosmetics and dermatological products began to blur. Cosmetic problems such as aging, uneven skin pigmentation, slack skin, cellulite, sensitive skin, oily skin, and dryness were identified and agents were sourced or developed to address these conditions. These skin disorders were often associated with conditions such as sunburn, acne, and the need for topical analgesia, etc. Cosmetics turned more to medicine for its resources, and dermatology became a source for agents that could provide either a marketing or performance advantage.
As the number and potency of functional materials increased, there arose a need to control the delivery of these agents in order to mitigate potential irritation, target their transfer to the desired location in the skin, or protect environmentally unstable materials for a commercially viable period of time. Again, the personal care market borrowed from the latest advances in medical research. Table 1 is a summary of some of the major delivery systems currently being used in the personal care market place, the types of active they carry, and their primary benefit.
Table 1: Delivery Systems Most Commonly Used in Personal Care
Classification | Description | Diameter | Materials Carried |
Liposomes | Phospholipid-based | 100-500 nm | Hydrophilic and hydrophobic actives |
Nanodispersions | Phospholipid-based micellular | 100-500 nm | Hydrophobic actives |
Vesicles | Surfactant-based vesicles or micelles | 100-500 nm | Typically hydrophobic actives |
Polymeric | Crosslinked acrylate or allyl methacrylate polymer | 10-500 micron | Typically hydrophobic actives |
Microencapsulates | Aldehyde crosslinked protein | 100-5000 micron | Typically hydrophobic actives |
Encapsulates | Crosslinked guar, alginate or other carbohydrate polymer | 5-500 micron | Typically hydrophobic actives |
Entrapment/Clatharate | Clatharate of cyclodextrin | N/A | Hydrophobic actives |
Linked | Active ingredient is covalently or ionically linked to polymeric support | N/A | Hydrophilic and hydrophobic actives |
The trend toward even greater performance in personal care products will continue as we move further into the 21st century. New, more potent therapeutic agents are being sourced from the fields of biotechnology, pharmaceuticals, and botanicals. Materials such as enzymes, growth factors, antioxidants, cytokines, DNA, genetic promoters, epigenetic modifiers and other sophisticated materials are already being evaluated in the research facilities of leading manufacturers and suppliers. These agents, though more effective than previously used actives, are often sensitive to environmental conditions such as oxygen, heat and light. Thus, there will be a need for equally sophisticated delivery systems that will maintain or enhance the efficacy of these sensitive actives from their formulation and environmental surroundings.
While drug delivery systems have received much attention because of their potential, what is often overlooked is the vehicle into which these delivery systems are incorporated. The latter part of this chapter will focus on the proper selection of the vehicle into which the delivery systems are added, in order to ensure their performance is not compromised. The chapter will also explore a new approach to vehicle development that is complementary to most, if not all, delivery systems. This new approach is actually a true innovation in formulation science. The technology employed offers virtually unlimited aesthetic and form modification capabilities that will enable the user to truly enjoy the experience of applying the product. This new approach is called Sub-micron Micelle-Based Formulating.
Clearly, the preferred cosmetic and personal care vehicle for topical application contains both aqueous and anhydrous phases. Such products have virtually unlimited aesthetic properties and can be applied in many forms such as serums, lotions and creams. However, these components are generally incompatible with one another unless an agent is added that more significantly reduces the interfacial tension between the oil and the water phases. To do this, it is necessary to change the native properties of the oil phase and the water phase to make them more compatible with one another. This phenomenon allows the formation of a two-phase system in which one of the phases (e.g., the “oil”) is suspended in the other (e.g., the water). Such ingredients are called “surface active agents” (“surfactants”). A special sub-category of surfactants is called an emulsifier. These materials not only lower the interfacial tension at the oil/water interface but, with the input of shearing energy, they enable the formation of droplets of one phase within the other. Such emulsifiers have a wide range of surface-active properties. When carefully selected, they can stabilize the incorporation of oil into a water phase or water into an oil phase. The resulting product is called an emulsion. In many cases such emulsions are prepared by heating the oil and water phases to a temperature of 70o C or greater before combining the two phases. The purpose of heating the phases is to ensure that all waxes used are melted, and that the two phases have a low enough viscosity so the two phases can mix freely. The oil and water phases are typically mixed together until they achieve a homogeneous appearance. Thereafter, they are slowly cooled to ensure the formation of appropriately small-sized droplets. It is essential that the droplets be very small in order to ensure the stability of the emulsion since, in these cases, Brownian motion will retard sedimentation. Such emulsions typically have a homogeneous, opaque, white appearance. They provide a smooth, pleasant feel upon application to the skin, hair, or other epithelial surfaces. In fact, the fields of surfactant chemistry and emulsion science have become a major disciplinary area that a competent cosmetic chemist must master in order to be a successful formulator. The proper use of surfactants to form all of the various types of useful emulsions can become a totally engaging, lifelong pursuit. The vehicle formed by the combination of an aqueous phase with an anhydrous phase will be the primary focus of the remainder of this chapter.
The introduction of surfactants to the cosmetic industry has provided a “double-edged sword” for formulators. Although the many different types of surfactants have yielded a vast array of cosmetics with very desirable aesthetic properties, the issues associated with their use have not been properly addressed. To the formulator, the development of emulsion-based products is replete with problems. Such development is a time consuming process. Further, these issues are generally limiting towards the goal of achieving desirable aesthetic properties. These issues can produce thermodynamically unstable, non-reproducible and difficult-to-scale emulsions in the manufacturing process.
It is easy to understand, therefore, why the time to develop a traditional emulsifier-based product is so lengthy. Seldom does a formulating company’s Marketing department or Business Development function request exactly the same formulation. Generally, new marketing concepts will necessitate a change in composition from prior art. This change can cause a cascade of undesirable events. Different aesthetic properties are also frequently requested by Marketing in order to generate new products with new claims. When changes to either the aqueous phase or oil phase are made, the emulsifier blend, which was effective in previous systems, generally must be altered. Altering the emulsifier blend may result in a change in one or more aesthetic, performance, or safety properties. Immediate stability of the composition is often compromised as a result and, worse, such instability is not usually identified until the second or third month of accelerated stability testing. This behavior may indicate a potential problem with the long-term shelf life of the product, and it is insidious since it requires either re-balancing of the emulsifier ratios or a change in the emulsifiers selected. This has forced the industry to develop methods to predict the degree of hydrophobicity of the oil phase in order to marry it with the necessary changes to the water phase in order to permit the formation of a stable emulsion. Systems such as the HLB (Hydrophile-Lipophile Balance) have been devised. This assigns a relative numerical value to the degree of lipophilicity of a given oil, which enables the formulator to select the necessary emulsier, or blend of emulsifiers required. This approach was first developed by William Griffin who was employed by Imperial Cosmetic Industries (ICI). (1) This method has proven to be invaluable when preparing standard emulsion products. However, it becomes less predictive as the lipophilic phase becomes more complex through a mixture of soluble oils and is less relevant where blends of insoluble lipophilic agents are used.
Generally, a sequential approach to problem resolution will result in an extended time to develop a product. This will result in a delay in the projected launch date that can cost the organization millions of dollars in anticipated revenues. As a consequence, the formulator is best served by trying to anticipate potential issues. Multiple batches, having several ingredient variations, are typically prepared in order to address any unexpected contingencies. This process is filled with unnecessary redundancy and is generally unacceptable in commercial practice. Compounding the above mentioned issue is the effect that processing can have on the outcome of a batch. Emulsion stability is dependent on a variety of parameters such as the zeta potential, particle size, crystal formation, and water-binding activity (2) of the ingredients employed to achieve the desired rheological properties of the product. These parameters are dependent on the temperature to which the oil and water phases are heated, the rate of heating, the method and rate of mixing of the phases when combined at elevated temperatures, and the rate of cooling. Most emulsions require heating to insure that all higher melting point materials, such as waxes and butters, are completely melted, dissolved or dispersed in the appropriate phase.
Further, many raw materials with unique aesthetic properties cannot be emulsified easily, if at all. Useful molecular weight silicones, silicone and hydrocarbon-based gels, and fluorinated compounds are all very difficult to incorporate into a stable emulsion system.
Traditional emulsion systems also create difficulties in manufacturing. The need for heating and cooling systems, specialized high and low-shear mixing, and assorted additional processing devices makes the manufacture of emulsion systems very capital intensive. Further, the equipment specifications and energy requirements will vary from country to country. This situation will cause a modification in the processing variables thereby making it almost impossible to have a truly “global” manufacturing protocol. The energy needed to process such products can be significant and undoubtedly will add to the final cost of the finished unit. This is especially true in Europe and Asia where the price of energy is very expensive. Similarly, there is a long duration of time required to prepare a batch. It can take from 5 to 24 hours, or more, to complete the processing of emulsions depending on the batch size and number of sub-phases required. This reality requires intensive labor and energy that adds to cost to the final product.
The need for high temperature water or steam to heat the phases of the batch can cause damage to heat sensitive actives such as retinoids and proteins. Prolonged heating of certain materials can accelerate the reaction of the active agent with other components in the emulsion, or with air, if the material is oxygen sensitive. For example, the exposure of unsaturated hydrocarbons, such as vegetable oils, to air at high temperature can cause oxidation and lead to both rancidity and an undesirable color change. This is especially true where there is a growing consumer demand for products that are naturally-based from sustainable/renewable sources.
As indicated above, the complexity of the manufacturing procedure for personal care emulsions, and its dependence on many processing variables, leads to frequent quality issues. This is especially true with respect to the product’s final textural and rheological properties. If any factors such as the heating, cooling or mixing rates are not carefully duplicated, the material prepared may have different properties than the preceding batches of the same product! As a result, the stability of the emulsion may vary from batch to batch.
Often, the difference of a single parameter is significant enough to cause the product to be outside the established optimum specifications. Inevitably, batches have to be either discarded or reworked. The lack of reproducibility is especially problematic when the product contains a physiologically active agent. Lack of reproducibility, due to manufacturing variations, can affect product performance and decrease consumer satisfaction. It also results in products having undesirable aesthetic properties that the user may perceive as a lack of quality. This will ultimately lead to consumer dissatisfaction, or reduced compliance in product use.
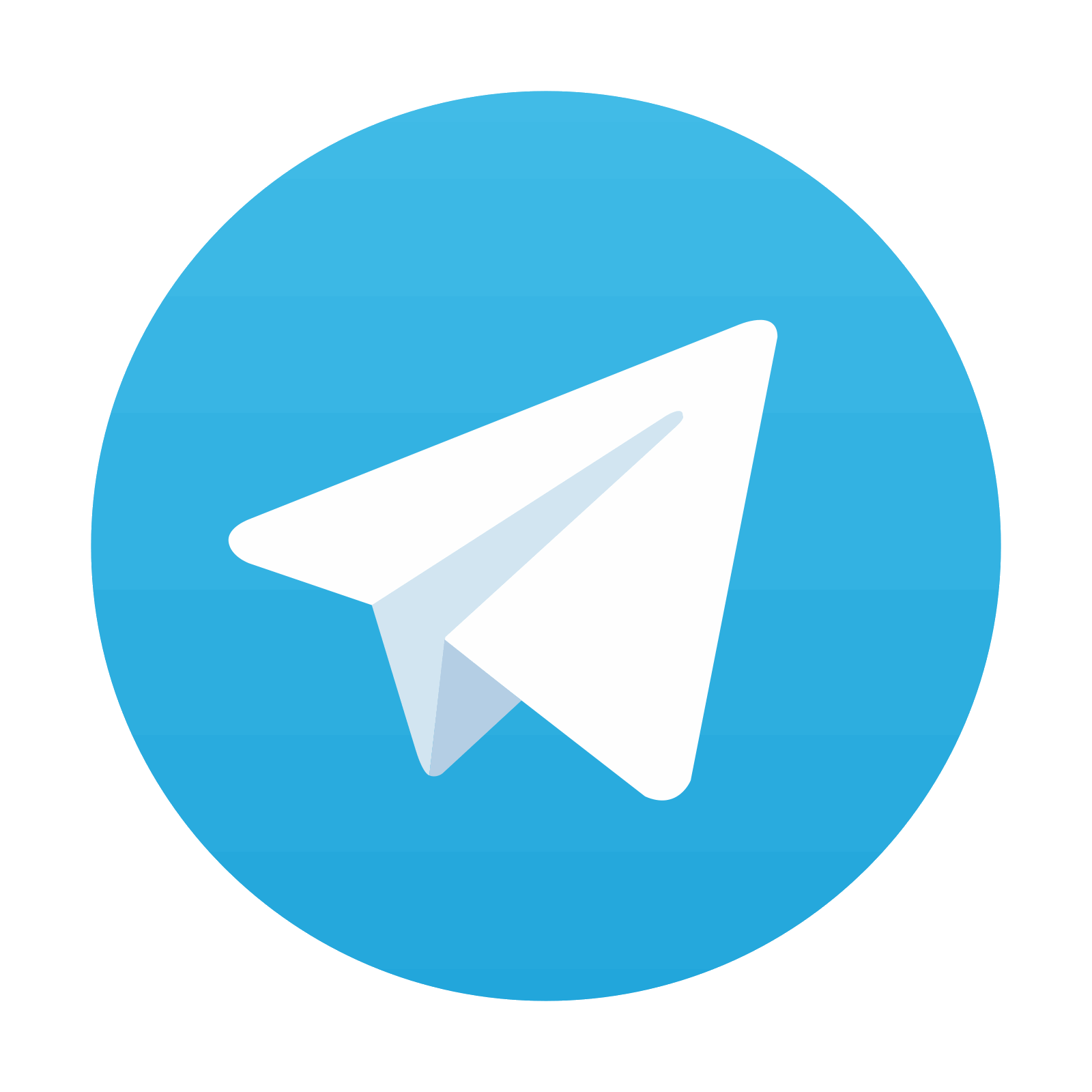
Stay updated, free articles. Join our Telegram channel
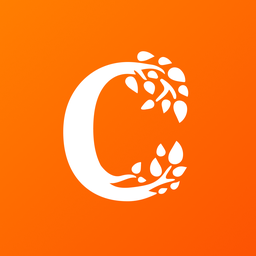
Full access? Get Clinical Tree
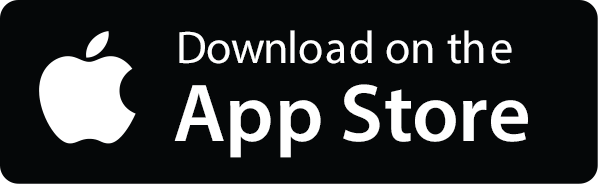
