The aerosol industry experienced significant growth until 1978, when the use of chlorofluorocarbons (CFCs) for non-drug applications was essentially banned, at least in the United States.
The subsequent introduction of propellants with reduced ozone-depletion potential provided some impetus to the marketing of cosmetic aerosols. In recent years, concerns about the introduction of volatile organic compounds (VOCs) into the atmosphere have created additional restrictions on the aerosol industry.
The word aerosol is a generic term in colloid chemistry for finely subdivided liquid or solid particles dispersed in, and surrounded by a gas. The particles/droplet size should be smaller than about 50µ and usually is less than 10µ in view of an inhalation concern. The Consumer Specialty Products Association CSPA (formerly known as the Chemical Specialties Manufacturers Association) broadly defines an aerosol product as a self-contained sprayable product in which the propellant force is supplied by a liquefied/pressurized gas. Scientifically, the term “aerosol” refers to a suspension of liquid or solid particles in a gas that is the result of dispensing a product from a container under pressure. Nevertheless, the commonly used terminology defines aerosols as delivery systems for foams, pastes, powders, and the like from a pressurized container.
14.2.3 PRINCIPLE OF AEROSOL TECHNOLOGY
The concept of dispensing a product from a container under pressure is illustrated in Figure 14.2.1. Depression of the actuator opens a valve that otherwise seals the contents of the container from the lower ambient external pressure. The pressurized, liquefied, or gaseous propellant then expands and forces the product up into the dip tube for dispensing into the surroundings [1].
Are those in which the concentrate (product) and the propellant are dissolved in each other to form one single liquid phase. Examples of homogenous phase systems include, but are not limited to: anhydrous hair spray, spray cologne, etc.
Are those where the concentrate and the propellant form a temporary dispersion or uniform mixture liquid phase for a period of time. Such systems may separate upon prolonged standing into both a liquid and a vapor phase. Examples for heterogeneous systems include hair-styling mousse, antiperspirant, etc. Heterogeneous systems require a “Shake Well Before Use” statement on the label.
Are those in which the concentrate and the propellant are filled into separate chambers within the aerosol container. In such systems, the two components are not mixed and only the concentrate is dispensed, in a manner similar to a post-foaming shave gel. Examples include ShaveGel and sunscreen spray.
Later in this chapter there is a brief discussion on the barrier pack alternative aerosol system.
14.2.5 COMPONENTS OF AN AEROSOL CONTAINER
A finished aerosol product includes the product, the propellant, the container, the valve with attached dip tube or with an inverted body that only dispenses when actuated in the upside-down position. In common practice, the typical arrangement of these components is as shown in Figure 14.2.1.
Figure 14.2.1: Components of an aerosol dispensing system; the propellant in this case is lighter than the product and is not miscible with it. Headspace is not specifically shown. (reprinted from Harry’s Cosmeticology 8th Ed.)
Aerosol containers must be designed to contain the product and the propellant. This means that the shape of the container must be maintained despite the pressure differential across the inside and the outside wall. The container must resist deformation and assure product integrity even after prolonged contact with the propellant and the product. The materials of choice are tin-plated steel, aluminum, glass, and—in some countries—polyethylene terephthalate.
a. Three-Piece Tin-Plated Steel
For the manufacture of this type of container, steel plate of the desired thickness is plated with tin to produce a shiny nonporous coating. Three-piece steel containers are decorated and coated flat before coiling and assembly. A variety of organic coatings may be applied to enhance the stability of the metal against corrosion. Such cans are available in different sizes and in varying levels of tin coating.
In the United States, steel-can height dimensions are described in inches. For example, a can designation of 202 × 509 identifies a can diameter of 2 and 2/16 inches, and a can height of 5 and 9/16 inches.
These cans are manufactured by impact extrusion and wall ironing. As a rule, protection by the tin plating is less reliable than that obtained in three-piece cans. As increasing attention has been paid in recent years to ozone-layer depletion, regulatory changes have aimed at reducing the Volatile Organic Content (VOC) of solvents used in such cans. As a result, there has been a significant shift in development of products packaged in aerosol cans towards more water-based products. DS Container (www.dscontainers.com) now offers a two-piece extruded steel can with a nylon-type internal lining. This approach is quite useful since the aerosol contained is more compatible with a variety of water-based products.
Most aluminum cans are produced from 99.5% pure aluminum by impact extrusion. Aluminum cans have aesthetic appeal, and with today’s technology, shaped cans are readily available. With the current rising cost of steel, the price for aluminum aerosol cans is now comparable to that of steel cans.
Most experts agree that aluminum cans are better suited for products that are water-based than tin-plated steel cans.
Examples of such aqueous products include those with a pH range of 5.0 (acidic) to 7.0 (neutral) and include, for example, mild cationic hair-styling mousses.
Aluminum cans, like tin-plated steel cans, are shatterproof and can withstand a wide range of pressures. Aluminum can be provided with outside or inside curls and various shoulders to accommodate a variety of overcaps or spray-through domes. They require corrosion-resistant internal coatings such as organosols (recently banned in the EU) for water-based products, epoxy phenolics, or polyamide imide (for water-alcohol and dimethyl ether, i.e., DMF-containing formulas). DMF/water-based formulas have been patented for their ability to reduce flammability. Regardless of the can type, all metal cans shipped in the United States must conform to regulations concerning buckle pressure and burst pressure. In the United States these regulations are formalized and regulated by the Department of Transportation.
Both plastic-coated and uncoated glass aerosol containers are available. Uncoated glass containers must withstand pressures up to 15 to 20 psig at 21°C. They are useful for fragrances in hydro-alcoholic media and employ n-butane as propellant. If they are formed from clear glass, they are not useful for products sensitive to ultraviolet light, since the ingredients might react, degrade, or change color.
Color-coated glass containers provide ultraviolet light protection and—when fractured—retain glass fragments in the plastic coating. Though safer at higher pressures, the end-product pressure should not exceed 40 psig at 38°C. The thickness of the plasticized or polyvinyl chloride coating is about 0.035” to 0.055”.
Regardless of the type of coating employed, glass containers have aesthetic appeal and are rarely plagued by corrosion problems. They are available only with 20 mm openings, which restrict the valve-mounting cup to 20 mm as compared to the one-inch openings on metal cans.
Presently (2013) in the United States, the use of polyethylene terephthalate (PET) for aerosol containers is not permitted because of the tendency of propellant permeation through the container wall; however, laminated PET containers are under consideration. The use of PET bottles is allowed in some other jurisdictions.
Without a fully functional valve, a marketable aerosol cannot be prepared. As a result, many types of valves are available for controlling the flow of product from the filled container. Aerosol valves may be vertical-acting, toggle-acting, or inverted acting. They may also have metering capability, and may be capable of delivering foam liquids like shaving creams or dry antiperspirant sprays.
a. The Male Valve (see Fig. 14.2.2)
The male valve includes the stem, stem gasket, spring, body or housing, dip tube, and mounting cup. The valve must not only seal the product from contamination from the environment but also preclude loss of the propellant. The stem is commonly made of a rigid plastic (nylon, acetal, or polyester); it is slotted or barbed to hold the actuator. The stem gasket is made of a flexible polymer, such as buna, neoprene, or butyl rubber. The shape of the stem can be varied to allow rapid filling of propellant “through the stem.” The spring is 302 or 304 stainless steel, with five to seven spirals. The housing may be provided with a vapor tap that allows dispensing in a position in which the dip tube does not contact the product. The dip tube is commonly prepared from polyethylene or polypropylene and is firmly attached to the housing. Finally, the mounting cup, which is crimped to the aerosol container curl, is made of the same metal as the container. The mounting cup may include a cut gasket or other sealing mechanism, such as a polyethylene sleeve gasket, to ensure a hermetic seal when the valve is crimped to the container. If the product is dispensed only when the container is inverted, a dip tube may not be required, as, for example, in some shaving gels and styling mousses.
Figure 14.2.2: Diagrammatic view of a typical aerosol valve, showing the key components (Courtesy of Precision Valve Co., Yonkers, N.Y. reprinted from Harry’s Cosmeticology 8th Ed.)
b. Female Valve (see Fig 14.2.3)
The female valve has similar components as the male valve except without the valve stem. The stem portion of the valve with various orifices is fabricated into the actuator configuration to control the flow of products. Together with different inserts, they govern the spray rate and pattern. Without the valve stem, products and propellant can be filled through the wide-open body at very high speed.
Figure 14.2.3: Female Valve
(Courtesy of Seaquist Perfect Dispensing)
The selection of the stem gasket is critical for proper operation of the aerosol unit. For the sake of compatibility and functionality, the formulator has to make a selection from nitrile, neoprene, buna, butyl, or viton rubber. This choice is as important as the selection of propellants or of the solvent used and may require extensive stability testing.
Are designed to deliver the product at a rate acceptable to the consumer and appropriate to the product. The criterion is the spray (or delivery) rate, which must remain inviolate throughout the life of the product. Foam valves provide unobstructed product passage through the body and stem orifice.
With self-cleaning stem-wiping action allow smooth passage with no hold-up of solids to interfere with valve operation.
For water-based products or products require finer breakup of particle size, and they may require two entrances to the chamber in the valve housing; one of these taps the vapor phase, which admits only propellant vapor, and the other provides access via the dip tube. This type of valve, known as a vapor tap valve, helps to break up particles when the product is actuated. Such valves are sometimes provided with a so-called Aquasol piece, in the valve body; the exiting propellant/product mixture spins the piece, which helps breakup of larger particles.
Vapor tap valves are required for spraying in the upright and inverted positions.
Reduce the product discharge rate and deliver a drier product. Formulators should recognize that such valves increase the discharge of propellant and may modify the spray pattern. It is essential to make certain that there is sufficient propellant in the unit to ensure uninterrupted discharge until empty.
Include a holding chamber in the valve body for delivery of a predetermined quantity of the product. They are employed primarily for costly perfumes and therapeutic inhalers.
Tight attachment of the valve to the container is essential if leakage is to be avoided. Latent leakers are those cans that pass the water bath test but may begin to leak after storage. Successful crimping requires adherence to tight dimensional specifications for different valve cups attached to different cans.
Large-diameter aluminum from 50 mm and larger sizes might have “eye-lashing” from the curl-forming stage. A lathe-cut gasket is used in combination with a shave curl. The curl is shaved at an angle to form a sharp edge so that the lathe-cut gasket has a sure sealing point, which will ensure tight leakproof crimping.
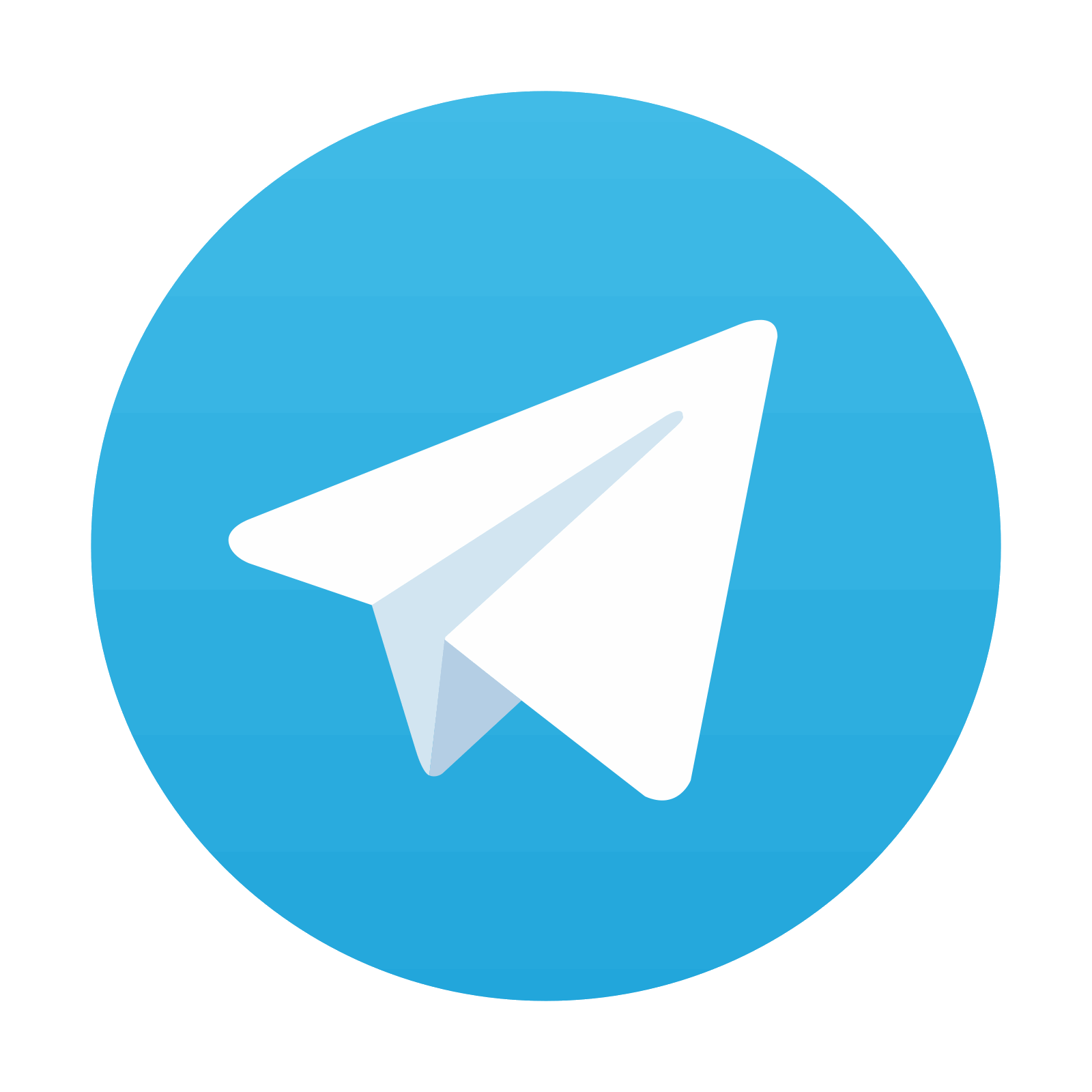
Stay updated, free articles. Join our Telegram channel
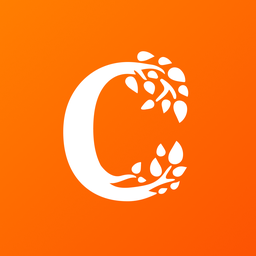
Full access? Get Clinical Tree
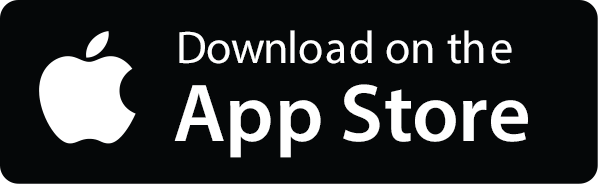
