CONSUMER PERCEPTION
Authors
Lisa Gandolfi, Ph.D.
Clariant Corporation
Technical Manager, Consumer Care North America
625 East Catawba Avenue
Mount Holly, NC 28120 USA
Ramiro Galleguillos, Ph.D.
Lubrizol Advanced Materials Inc.
Senior Research Associate
9911 Brecksville Rd.
Brecksville, Ohio 44141 USA
ABSTRACT
All consumer product formulations have an inherent rheological character that is dictated by the raw materials used and how they are combined in the formulation. The rheological character is a description of the flow behavior over a range of shear rates and with the passage of time while being sheared. There are many parameters that contribute to the overall rheological character of a formulation. Viscosity is the most common rheological parameter encountered in formulation. Said simply, viscosity is the measure of flow of the fluid, over a range of shear rates from very low (like sitting in a container, or being poured) to very high (like being applied to the skin upon rubbing). Sometimes the viscosity is constant over the range of shear rates and with the passage of time. At other times, the viscosity may increase or decrease with shear and with the passage of time. Yield stress is a critical rheological parameter for imparting stability to emulsion formulations and to optical effects formulations, such as cleansers or hydroalcoholic formulations that have some type of optical effect, such as beads or air bubbles. Viscoelasticity is a third rheological parameter. Viscoelasticity is the balance of the viscous and elastic components of a material. It impacts the formulations visual aesthetic when it is at rest and the pick-up and cushion of formulations during rub-in. The array of formulation attributes that are affected by its rheological character makes the design of the rheological behavior of a formulated product a crucial step in order to make a product behave in the desired way in the consumer’s hands and during use.
4.2.2.2 Rheological Parameters
c. Viscosity of polymeric rheology modifiers
4.2.2.3 Synthetic Polymeric Rheology Modifiers
a. Modified Sulfonic Acid (AMPS®) Polymers
b. AMPS® Polymers Rheological Properties
d. Polyacrylic Acid Polymers Rheological Properties
e. Alkali Swellable Emulsion Polymers – ASE/HASE Polymers
f. Rheological Properties of ASE/HASE Polymers
4.2.2.4 Rheological Properties And The Consumer Experience
4.2.2.5 Polymeric Rheology Modifiers In Emulsion Formulations
a. Yield stress for emulsion stability
b. Relationship between rheological properties
and the sensory experience
g. Correlation of Rheological Measurements and
Consumer Perception in Emulsion Formulations
4.2.2.6 Polymeric Rheology Modifiers In Hydroalcoholic Formulations
4.2.2.7 Polymeric Rheology Modifiers In Optical Effects
Cleansing Formulations
In this chapter we describe some of the key rheological modifier polymers, their structure in general, and the variables of structure that can be built in in order to provide a range of behavior in cosmetic and personal care formulations.
In many formulations, the rheological properties provided by the primary functional materials can provide the desired physical behavior and flow properties for the formulation. For example, an emulsion may be stable and sufficiently thickened only by the inclusion of emulsifiers and oils, and this resulting formulation will have its own unique rheological profile. Often, however, the primary functional materials of a formulation, such as emulsifiers and oils, are not sufficient to impart long-term stability, thickening, and a desirable rheology. In this case, polymeric rheology modifiers are typically employed. Polymeric rheology modifiers have the ability to impact multiple aspects of formulations, including formulation stability and the product’s full sensory profile. The typical rheological parameters that impact personal care formulations are viscosity, yield stress, and viscoelasticity. It is critical to choose a polymeric rheology modifier that can help to deliver the desired product aesthetics to your formulation. The most commonly used synthetic polymeric rheology modifiers are modified sulfonic acid–based polymers, polyacrylic acid–based polymers, and alkali swellable emulsion–type polymers.
4.2.2.2 RHEOLOGICAL PARAMETERS
A primary function of polymeric rheology modifiers is to provide increased viscosity of the solvent, such as water. Viscosity is a measure of the resistance to flow when a shear stress is applied. For ideal viscous fluids, the value of the ratio of the shear stress, t, to the corresponding shear rate, g., is a material constant called the apparent viscosity, h. These kinds of fluids are often referred to as Newtonian fluids. One example of such a fluid is polydimethyl siloxane. Many types of fluids in personal care exhibit a pseudoplastic or shear-thinning behavior with the applied force. In these fluids, the value of the ratio of the shear stress to shear rate decreases with the shear rate. Equations 1 and 2 and Figure 5 illustrate these behaviors:
With rare exceptions, Newtonian and pseudoplastic fluids are the two most common fluid types encountered in personal care formulations at room temperature and under typical conditions of usage. Note, however, that a large variety of rheological behavior, such as plastic, pseudoplastic, dilatant, rheopectic, thixotropic, is found in many other industrial fluids and formulations and has been extensively documented in the literature (1).
Graphical examples are best suited for illustrating rheological behavior, although there are numerous mathematical models that are used to describe such behavior (2) (3). Two types of graphs are commonly used. One is a plot of apparent viscosity versus shear rate as shown in Figure 1:
Figure 1. Typical graphical representation of viscosity versus shear rate for aqueous personal care formulated products.
The other way to graphically describe the rheological properties of a liquid formulation is to plot the shear stress versus shear rate data as shown in Figure 2. In this way data obtained at various temperatures and at varying concentrations of the rheology modifier and other formulation ingredients can be obtained and studied to fully characterize the rheological properties.
Figure 2. Typical graphical representation of shear stress versus shear rate for aqueous personal care formulated products.
A number of aqueous formulations in personal and home care obey the rheological flow behavior described in Figures 4 and 5. These include shampoos, bath gels, body washes, liquid soaps, hair gels, toothpastes, skin creams, lotions, pomades, etc. Many of these formulations are emulsions or contain dispersed solid matter such as beads, mica, pearlizing crystals, seeds, etc. However, from a rheological viewpoint, the difference among these products is not essential; it is more of a quantitative than qualitative nature.
The viscosity of aqueous formulations in personal care is typically measured using various types of rotational and oscillatory rheometers. Rotational rheometers typically measure the torque on a probe such as a rotating plate, cylinder, or a spindle of certain specific geometry, in contact or immersed in the test fluid. The measured torque is correlated to viscosity by the instrument’s processor. Typical measuring systems of the rotational type include a) concentric cylinders, b) cone-and-plate, c) parallel-plate and d) relative measuring systems. Brookfield rotational viscometers are relative measuring systems (4). They are extensively used to measure the viscosity of aqueous compositions of various kinds. They are inexpensive and simple to use; however, they only measure relative viscosity values or instrument-dependent values since the viscosity is measured with a specific spindle with no information of shear rate, which is required according to Newton’s Law in equation 1. Oscillatory rheometers are instruments in which the probe instead of rotating is oscillating according to a periodic oscillatory motion, such as for instance a sinusoidal motion of either constant amplitude or frequency. The rheological information obtained includes a number of parameters that assess the viscous and elastic components of the formulation in terms of the elastic or storage modulus (G’), the viscous or loss modulus (G”) and the loss factor (tan δ). One of the main advantages of this system is that the strain or deformation imposed on the fluid is very small. Regardless of the instrument used, temperature control is essential to perform accurate measurements, particularly in the case of aqueous formulations whose viscosity can significantly vary with a change of only ±1°C.
c. Viscosity of polymeric rheology modifiers
In order to understand the different thickening mechanisms of polymeric rheology modifiers it is necessary to review the basics of viscosity in relation to polymer solutions. When a fluid is at rest, solvent molecules move rapidly under Brownian motion. When a fluid is flowing, solvent molecules move rapidly in the direction of flow. A low viscosity fluid is obtained when the solvent molecules are undisturbed and able to flow rapidly. When solvent molecules are disturbed and need to flow around or through an obstacle, they move along a longer path or more slowly, both of which decrease the rate of flow of the fluid. The resulting macroscopic behavior, in both cases, will be that of a high-viscosity fluid.
Polymers in solvent exhibit a hydrodynamic volume. The hydrodynamic volume is the effective volume of space that the polymer fills. The chemical composition of a polymer will dictate the nature and strength of the interactions between that polymer and its solvent. In a good solvent, the polymer has strong interactions with the solvent and exists in a more expanded conformation. This expanded conformation takes up more effective space and therefore the hydrodynamic volume of the polymer is greater. Solvent molecules flowing around or through a polymer with a greater hydrodynamic volume will move more slowly and will result in a high-viscosity fluid. As the hydrodynamic volume of a polymer in solution increases, so does the viscosity. By contrast, in a poor solvent, the interaction of the polymer with the solvent is unfavorable, so the polymer interacts preferentially with itself. This results in a more collapsed conformation. This collapsed conformation takes up less effective space and therefore the hydrodynamic volume of the polymer is smaller, resulting in a lower viscosity. As a general rule, the greater the hydrodynamic volume of the polymer, the higher the viscosity of the fluid. Polymeric rheology modifiers impart thickening properties based on this principle of hydrodynamic volume.
Another primary function of polymeric rheology modifiers in formulations is to provide a yield stress or yield point. A fluid with a yield point begins to flow only when the external forces acting on it are larger than a certain shear stress commonly known as yield stress, τo. Equation 3 is a mathematical model of one such fluid from the many that have been proposed in the literature (5), where f (h, g.,τ) may be a mathematical function of the viscosity, h, shear rate, g, and shear stress,τ.
Yield stress is a critical parameter to providing stability in emulsions and suspensions. In practice, the yield stress of personal care formulations is used to estimate the suspending power of the rheology modifier and to predict the shelf life of a product. Yield stress can be measured or estimated in many ways. The procedure of choice to estimate yield stress must be validated for each formulation by conducting shelf life stability tests. In many instances the yield stress of a formulation can be estimated by linear extrapolation of the shear stress data to zero shear rate (6). For this, it is important to measure shear stress at the lowest shear rates possible under very well-controlled experimental conditions. The yield stress, τo, shown in Figure 5, was measured in a rotational viscometer and required shearing the fluid at very low shearing rates through the use of a very sensitive rheometer, under well-controlled experimental conditions.
Synthetic polymeric rheology modifiers may be linear or cross-linked polymers. Cross-linking of polymer molecules provides a network structure that imparts a particular yield stress to an aqueous formulation. The degree of cross-linking impacts the yield stress such that typically polymers with a higher degree of cross-linking exhibit higher yield stress.
A third critical rheological parameter in the design of personal care formulations is the viscoelasticity. Viscoelasticity is the balance between the viscous and the elastic components of materials. Elastic materials deform when subjected to an applied force, and the deformation reverses completely and spontaneously when the applied force is removed. Viscous materials deform when subjected to an applied force, and the deformation stops when the applied force is removed. Most practical materials exhibit both viscous and elastic behavior and are referred to as viscoelastic. The balance of the viscous and the elastic components dictates the behavior of the material when a forced is applied (7).
Viscoelasticity can be measured with a rotational viscometer or a rheometer using an oscillatory technique. The relationship between the viscous component and the elastic component is described by the ratio, tan δ, of the storage or elastic modulus (G’) and loss or viscous modulus (G”), Equation 4.
When tan δ < 1, the elastic modulus is dominant. When tan δ > 1, the viscous modulus is dominant. A model strain sweep of a viscoelastic material is shown in Figure 3.
Figure 3. Model strain sweep of a viscoelastic material. G’ is the storage modulus and G” is the loss modulus.
4.2.2.3 SYNTHETIC POLYMERIC RHEOLOGY MODIFIERS
There are a variety of polymeric rheology modifiers available to the personal care industry, including both synthetic and natural polymers. Natural polymeric rheology modifiers derived from polysaccharides are discussed in more detail by Laba (8). Synthetic rheology modifiers are produced by polymerization of various types of monomers. Among the synthetic polymers, those prepared by free radical–initiated polymerization of vinyl, acrylate, or methacrylate and acrylamide or methacrylamide monomers constitute an important class of commercially available materials (9, 10). Depending on the monomers used, these polymers may be anionically or cationically charged; the anionic polymers being the most common synthetic rheology modifiers. The anionic charge in these polymers is typically provided by carboxylic and sulfonic moieties existing along the backbone of the polymers. Furthermore, and for convenience, these polymers are classified based on the form they are supplied as powder, liquids, emulsions (oil in water), and invert (water in oil) emulsions. In this chapter we will review the most commonly used synthetic polymeric rheology modifiers in personal care formulation: modified sulfonic acid–based polymers, polyacrylic acid–based polymers, or alkali-swellable emulsion type polymers.
a. Modified Sulfonic Acid (AMPS®) Polymers
Polymeric rheology modifiers based on modified sulfonic acid chemistry are often referred to as AMPS® polymers. The chemical structure of AMPS® is acrylamido-2,2-dimethyl propane sulfonic acid, and the AMPS® monomer is present in all AMPS® polymers designed for rheology modification. Different co-monomer structures are combined with AMPS® to provide a range of polymeric rheology modifiers. All of these polymers are chemically cross-linked, which provides, in part, their thickening ability. The range of different co-monomers leads to polymers that have different effects on many attributes provided by the polymer in formulations. These include, for example, electrolyte compatibility, thickening effects, and skinfeel sensorics.
Ammonium acryloyldimethyltaurate/VP copolymer (Aristoflex® AVC)19, Figure 4, is one of the most commonly used AMPS®-based polymeric rheology modifiers. The co-monomer in Aristoflex® AVC is vinylpyrrolidone (VP).
Figure 4. Ammonium acryloyldimethyltaurate/VP (Aristoflex® AVC) copolymer chemical structure.
Ammonium acryloyldimethyltaurate/beheneth-25 methacrylate crosspolymer (Aristoflex® HMB), Figure 5, is a hydrophobically modified polymeric rheology modifier, due to the beheneth-25 methacrylate co-monomer. The addition of hydrophobic groups to the AMPS® polymer chain provides a rheology modifier with an increased affinity for hydrophobic formulation components, such as oils and silicones. These polymers act as thickeners due to the cross-linking present in all Aristoflex polymers as well as efficient polymeric emulsifiers that can stabilize high oil loads without the need for traditional emulsifiers.
Figure 5. Ammonium acryloyldimethyltaurate/beheneth-25 methacrylate crosspolymer (Aristoflex® HMB) chemical structure.
There are distinct rheological differences between Aristoflex AVC and Aristoflex HMB due to the differences between the vinylpyrrolidone and beheneth-25 methacrylate co-monomers used in polymerization. Within the class of AMPS® polymers, a wide range of final chemistries is available based on selected co-monomers for use with the AMPS® monomer. Variations in the co-monomer structure and the cross-linking of the polymer chains significantly affect the thickening and yield properties of AMPS®-based polymers.
b. AMPS® Polymers Rheological Properties
AMPS®-based polymers have a permanent negative charge due to the sulfonic acid moieties in the AMPS® co-monomer, independent of pH. These polymers have a high degree of cross-linking so that although the charged sulfonic acid moieties repel each other, a permanent network structure exists. The negatively charged sulfonic acid moieties interact strongly with polar solvents, such as water, and the solvent swells the network structure to produce a larger hydrodynamic volume and thus thickening of the solvent-based formulation. This interaction of solvent and polymer is presented schematically in Figure 6.
Figure 6. Swelling of network structure of AMPS®-based rheology modifiers.
The co-monomer structure affects the strength of the polymer-solvent interactions as well as the degree of swelling of the network structure. Aristoflex polymers with higher charge density or more polar moieties will swell more quickly and reach a greater overall viscosity. As with all polymeric rheology modifiers, an increased polymer molecular weight results in increased thickening at lower polymer concentrations. The viscosity profile varies depending on these properties as shown in Figure 7.
Figure 7. Viscosity as a function of polymer concentration for AMPS®-based polymeric rheology modifiers Aristoflex® AVC and Aristoflex® Velvet, AMPS®-based terpolymer. Brookfield Viscometer Model RVDV-1, 20°C, 20rpm.
Aristoflex polymers with high degrees of cross-linking have a more elastic network, resulting in higher yield values and more elastic character. The tan δ as a function of polymer concentration for Aristoflex® HMB is shown in Figure 8 (11).
Figure 8. Elastic modulus, G’, as a function of frequency for 0.5%, 0.7%, and 1.0% Aristoflex® HMB in DI water. Values of tan δ are at 1s-1.
The yield point of Aristoflex® HMB in DI water is 0.3% (11). At all Aristoflex HMB concentrations above the yield stress, tan δ < 1 indicates a dominant elastic component. An increase in the concentration of Aristoflex HMB provided an increase in the elastic component of the gel.
An important class of anionic acrylate-based rheology modifiers is based on high-molecular-weight cross-linked polyacrylic acid technology. These polymers are commonly known by their INCI names carbomer and acrylates/C10-30 alkyl acrylate crosspolymer. They are used extensively in a variety of aqueous formulations including personal care, home care, pharmaceutical, and other industrial applications. Some examples are given on Table 1.
Table 1: Examples of Formulated Products with Carbomer and Acrylates/ C10-30 Alkyl Acrylate Crosspolymer
Body Care: Bath Gel, Body Wash, and Creams | Sun/After Sun: Tanning Lotions and Soothing Creams | Eye Color Cosmetics: Eye Shadow, Mascara |
Face/Neck Care: Creams and Soaps | Foot Care Creams | Hair Conditioner |
Shampoo | Hair Treatments: Hot Oils, Cold Waves, Straighteners | Lip Color Cosmetics: Lip Color, Lip Pencil, Rouge, Creams |
Hand/Nail Care | Shower Products | Eye Color Cosmetics: Eye Lash, Eye Shadow, Eye Liner |
Hair Styling: Gels and Pomades | Women’s Fragrances | Shaving Preparations: Foam and Gel |
Eye Care Creams | Face Color Cosmetics, Makeup | Women’s and Men’s Fragrances |
Liquid Soap and Detergents | Foundations, Fluid Illuminators, Glitter | Bath Additives |
Sun Care: Sunscreen Lotions, Creams and Spray | Face Color Cosmetics – Primers | Depilatory Products |
Hair Colorants and Hair Dyes | Body Color Cosmetics | Eye Cleansers |
The chemical structure of these polymers is shown in Figure 9.
Figure 9. A) Chemical structure of carbomer and B) Acrylates/C10-30 alkyl acrylate crosspolymer, R = C10-C30 Alkyl.
d. Polyacrylic Acid Polymers Rheological Properties
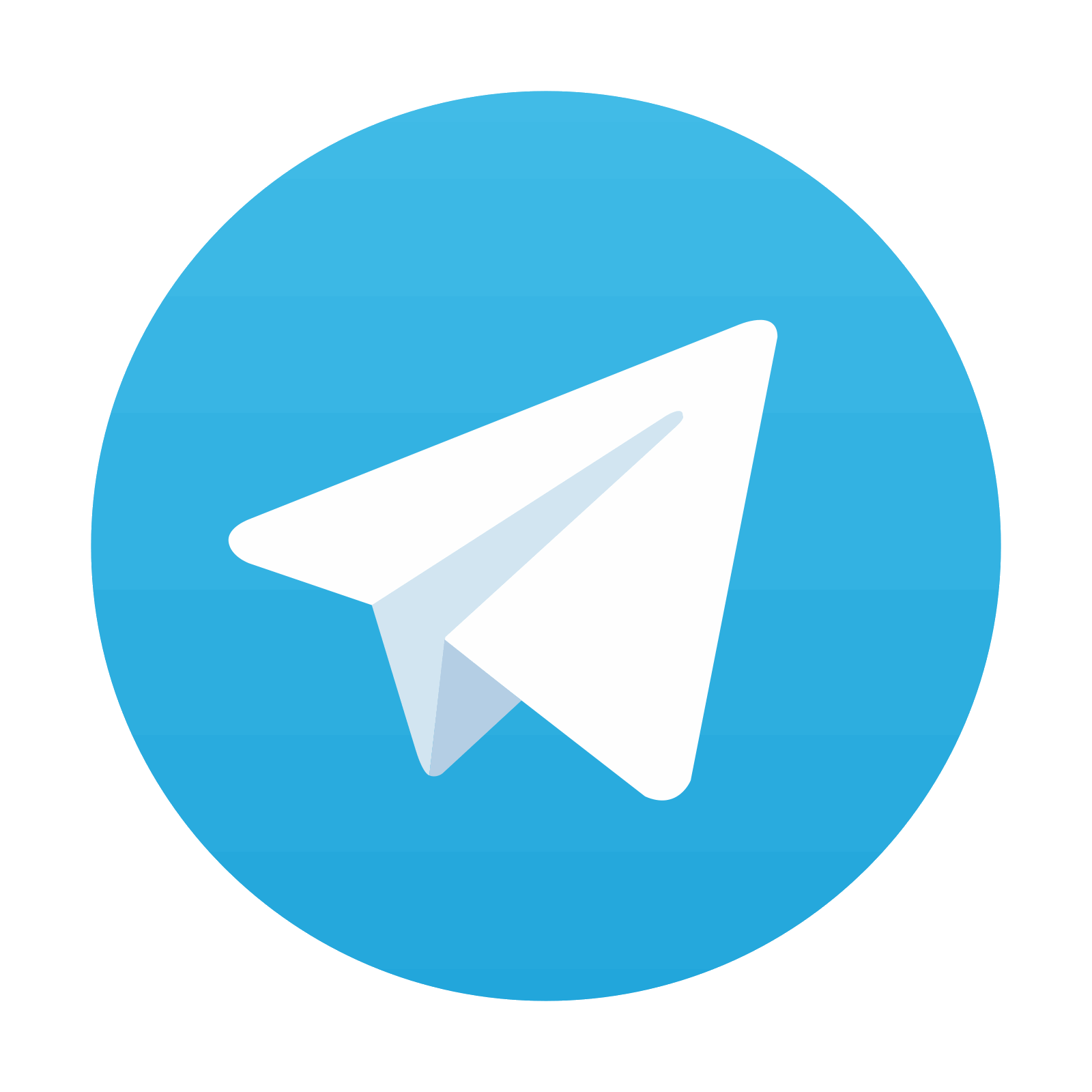
Stay updated, free articles. Join our Telegram channel
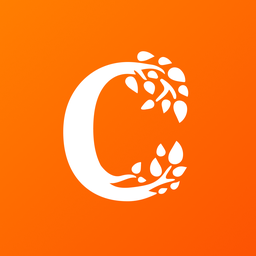
Full access? Get Clinical Tree
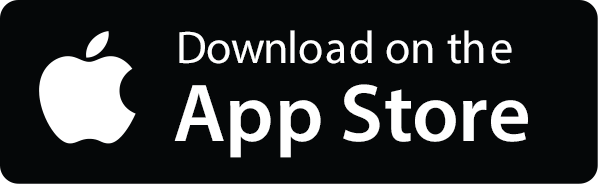
