CHAPTER 43 Surgical Options for Femoral Reconstruction
The Use of Modular Stems
KEY POINTS





Several treatment options are currently available for the reconstructive surgeon at the time of femoral component revision. Treatment options are primarily based on the extent of bone loss, the quality of available host bone and soft tissues, and the experience of the treating surgeon. Implant options include long-stem cemented implants,1 porous, extensively coated implants,2 modular extensively coated or fluted stems,3 impaction grafting,4 allograft-prosthetic composites,5 and tumor-type mega prostheses.6 The purpose of this chapter is to discuss the use of modular femoral stems in revision total hip arthroplasty.
The concept of modular implants has been used in total hip arthroplasty for over three decades. The concept of modular femoral heads and acetabular liners is well known to the orthopedic surgeon. McBride initially used the modular femoral stems in 1948.7 Bousquet and Bornard8 developed a proximal modular stem that featured a proximal body attached to a stem with a conical mounting post. The S-ROM femoral implant is the prototype of modular stems. The current S-ROM system is the fourth generation in the evolution of the Sivash stem initially introduced into the United States in 1972. The S-ROM consisted of a titanium alloy with distal flute fixation and a modular proximal sleeve providing rotational freedom.
In 1987 Wagner introduced a tapered, fluted, uncemented femoral stem design for revision total hip arthroplasty.9 He reported bone regeneration after the use of a cementless, tapered revision stem that was fixed in the diaphysis. The stem consisted of titanium alloy with a 2-degree taper with eight longitudinal ridges. This fluted stem design provided a high degree of rotational stability. Current design modular stems include both the Sivash10 and Wagner11,12 stem design concepts for femoral component revision, providing both a conical, tapered, fluted stem design and a cylindric design that can be either straight or curved. The cylindric stems are either smooth and polished with flutes or rough with porous or hydroxyapatite coating. The proximal bodies come in varying diameters and lengths to accommodate the diaphyseal-metaphyseal mismatch encountered at the time of femoral component revision (Fig. 43-1). Proximal bodies also come in various offsets and designs in order to maximize the proximal ingrowth and restore leg length.
BIOMECHANICS OF MODULAR STEMS
Canal-filling modular cylindric stems are used in a similar fashion as monolithic extensively coated stems that provide distal fixation. The primary disadvantage to the use of distal fixation with extensively coated stems is the inevitable proximal stress shielding that occurs over time. The use of tapered, conical, fluted stems is also popular. Owing to the conical, tapered design, these stems are loaded more proximally than are extensively coated, cylindric stems with distal fixation.13,14 Rotational stability using tapered, conical fluted stems is achieved by splines or flutes measuring 1 to 2 mm (Fig. 43-2).
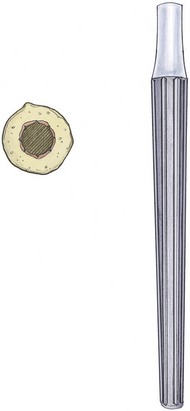
FIGURE 43-2 Tapered conical fluted stem with cross-sectional diagram demonstrating splines for rotational stability.
Initially designed modular femoral implants failed primarily at the Morse taper junction. The stress placed at the Morse taper with cyclic loading over time led to failure with fracture of the taper. The strength of the taper junction has been a significant concern because of the high stress concentration that occurs at this region. The Morse taper junction needs to adequately address cyclic loading to avoid fatigue failure and withstand fretting and corrosion. In a revision situation in which there is a lack of proximal host bone available for ingrowth, the Morse taper junction may bear significant loads, leading to failure. Improvement in the biomechanical properties of the Morse taper junction has been developed through the use of nitride impregnation, burnishing, and shot peening.15 Shot peening is a surface-hardening process through which small spheres of material such as steel or ceramic are used to bombard the taper junction. These spheres impart small indentations on the surface of the taper junction, which packs the surface molecules tighter, resulting in their greater compression. The shot peening process increases the fatigue strength by 33%. The current accepted guidelines established by the International Standards Organization (ISO) recommend that the Morse taper junction of modular femoral implants be able to tolerate 2300 newtons (N) or 517 pounds of cyclic load. Current design junctions exceed these guidelines and are able to tolerate 4450 N (1000 pounds).16,17 Ideally, the stresses placed at these taper junctions may be diminished over time as gradual proximal ingrowth occurs between the host bone and the proximal body of the implant.
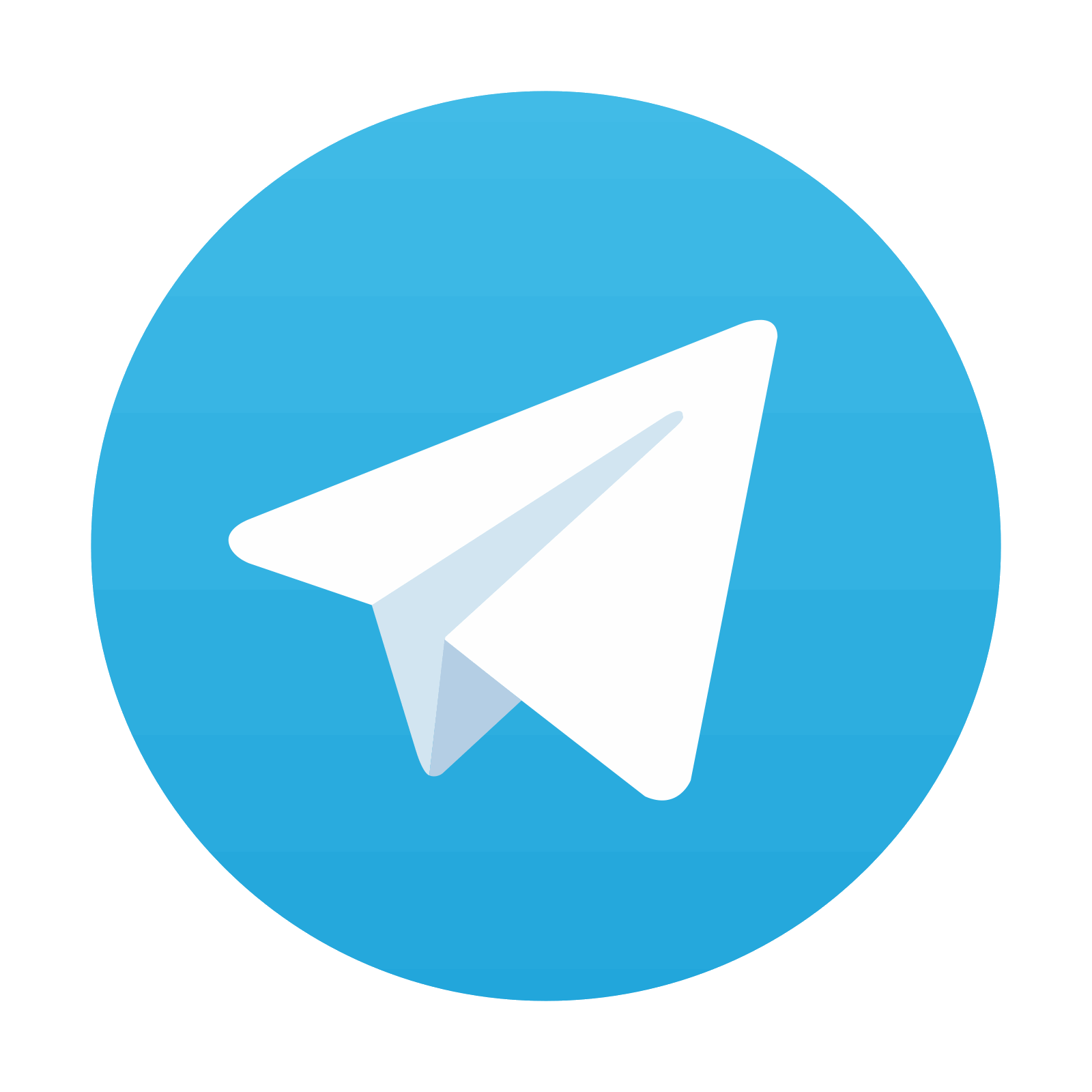
Stay updated, free articles. Join our Telegram channel
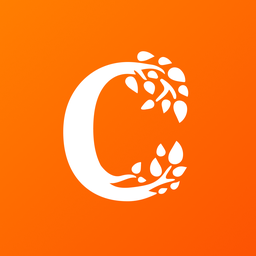
Full access? Get Clinical Tree
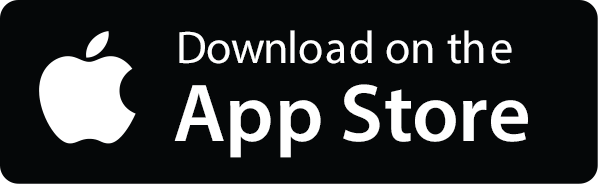
