41 The principles of dynamic stabilization in the treatment of activity-related chronic mechanical back pain has been described by one of the authors (DKS) in chapter 31 of this book. An ideal dynamic stabilization system should prevent abnormal high-load transmission through the disk and the facet joints by sharing the load while permitting normal motion.1,2 Load sharing is the principal mechanism of pain relief.3,4 However, load sharing and motion preservation both need further clarification.5,6 To maintain the nutrition and normal health of the disk and the articular cartilage of the facet joints, it is important that they bear a normal load and that motion is preserved. The device, therefore, should share only a partial load and allow a near normal load to be transmitted through the disk and the facet joints. Restriction of motion is neither the primary mechanism of pain relief nor is it desirable.7 However, to achieve load sharing, the device almost invariably causes some restriction of motion. How much load should be shared and how much motion should be permitted for ideal pain relief have never been determined. Perhaps these two parameters vary among individuals and also among motion segments in the same individual. It may be hypothesized that around a 20 to 40% load may be shared by the device, permitting the rest of the load to be transmitted through the facet joints and the disk. Motion restriction should be minimal if at all. However, it is more important that the device prevent any abnormal, sharp load across the disk and the facet joints throughout the range of motion (ROM), and that any abnormal quality of motion be prevented as well.1,2 Even a rigid fusion rod may fail if the segment does not fuse. How can the dynamic stabilization device survive fatigue failure in the presence of continued motion? The dynamic stabilization systems are inherently flexible and are designed to survive fatigue within a certain ROM and load. If at any stage during the ROM the device has to share a much higher load (say > 60% of the total load, when the device is meant to share only 30%) the device may undergo fatigue failure or loosening at the implant-bone junction. It is therefore important that load sharing be uniform throughout the ROM.8,9 The development of the Dynamic Stabilization System (DSS) (currently under development by the author (DKS), in collaboration with Abbott-Spine, Austin, TX) was based on these three principles: disk unloading by around 30%, minimal restriction of motion, and uniform load sharing throughout the ROM. The surgical principles dictating the design of the DSS were minimally invasive implantation and easy salvage in case of device failure. The predecessor of the DSS design was the Fulcrum Assisted Soft Stabilization (FASS) (Neoligaments, Leads, United Kingdom) described by Sengupta and Mulholland.10 The aim was to stabilize the spine and cause minimal restriction of motion, maintain a normal lordotic posture of the spine, and unload the disk. Biomechanical tests showed that, although the FASS system can unload the disk with minimal restriction of motion, the disk unloading and motion restriction were uneven. The FASS system produced restriction of flexion and too much unloading of the disk in flexion, whereas extension was unaffected. This predicted a possibility of excessive load being shared by the device in flexion, possibly resulting in early fatigue failure of the device or the implant-bone junction.10 Figure 41–1 The first-generation Dynamic Stabilization System (DSS-I) was a C-shaped titanium spring, made of a 4 mm diameter spring-grade titanium. The ends were thickened to 6 mm or fitted with a 6 mm diameter bushing for easy fixation to the regular pedicle screws, which can take a 6 mm rod. The author (DKS) subsequently designed a C-shaped titanium spring device described as the Dynamic Stabilization System-I or DSS-I11 (Fig. 41–1). Biomechanical tests with this device on cadaver spine showed a more favorable load-deformation curve and a uniform restriction of flexion and extension ROM by around 30% of normal range. This was important for fatigue resistance. An uneven restriction of motion in any particular direction would indicate excessive load sharing of the device in that direction of motion, which can lead to an early fatigue failure. However, when the effect of DSS-I was tested on cadaver spine, the disk pressure changes appeared to be unfavorable. The device unloaded the disk by 30% in flexion, which was desirable, but a complete unloading of the disk in extension, creating a negative disk pressure at the maximum extension. Normally, the disk pressure rises in both flexion and extension and is lowest at the early phase of extension (Fig. 41–2). A progressively increasing negative disk pressure with DSS-I indicated that the device shares increasing load toward maximum extension, which was not reflected in the load-deformation curve. Such excessive load sharing in extension would increase the possibility of an early device failure, and therefore this design was never implanted clinically (Fig. 41–2). The DSS-II was designed (Fig. 41–3) to improve on the uniform load sharing during both flexion and extension motions. This consists of an a-shaped coil made of a 4 mm diameter spring grade titanium rod with an outer diameter of 25 mm. The coiled section is elliptical rather than circular, so that the instantaneous axis of rotation of the device simulates a normal motion segment to ensure more uniform load sharing as mentioned earlier.8,9
Minimally Invasive Posterior Dynamic
Stabilization System
How Much Load Should be Shared and How Much Motion Restricted?
How Will the Device Survive Fatigue Failure in the Presence of Continued Motion?
The Design Rationale of the Dynamic Stabilization System
Clinical Study with the Dynamic Stabilization System (DSS-II)
Surgical Technique for Stabilization with the Minimally Invasive Dynamic Stabilization System
How Much Load Should be Shared and How Much Motion Restricted?
How Will the Device Survive Fatigue Failure in the Presence of Continued Motion?
The Design Rationale of the Dynamic Stabilization System
Stay updated, free articles. Join our Telegram channel
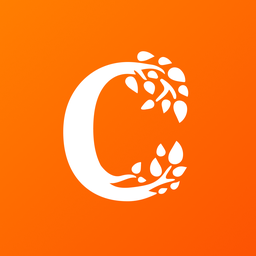
Full access? Get Clinical Tree
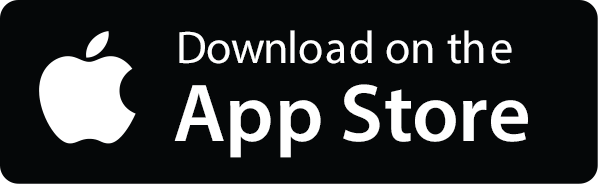
